Instructions for handling CLT Building Elements
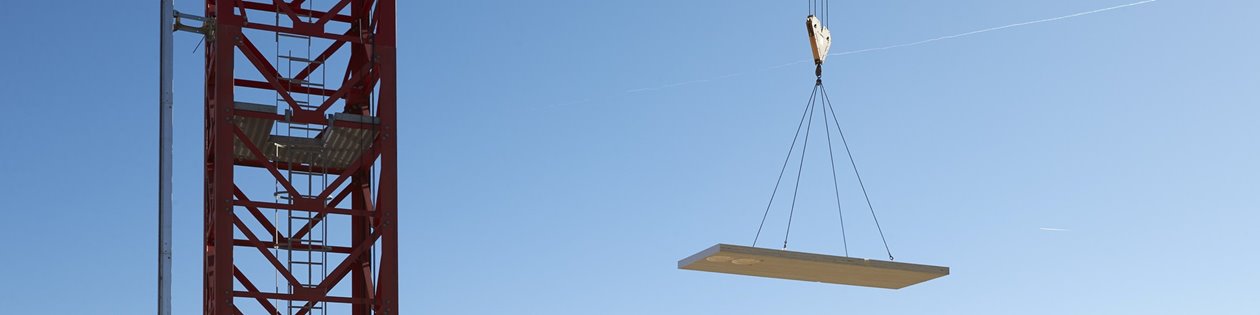
Swelash sling
Information and capacity values are taken from Swelash user instructions. For complete information, refer to Swelash’s own manuals.
These instructions should be seen as a summary of Swelash’s instructions. Södra is not responsible for incidents that occur due to the operator not following the manufacturer’s instructions.
- The instructions apply to lifting panels of specified dimensions in the factory and during assembly at the construction site.
- All lifts are dimensioned on the condition that load distributors are used during lifting so that all lifting points can be accounted for.
1. Intended Products
Lifting equipment: Swelash sling – For lifting and transporting prefabricated elements up to 8 tons.
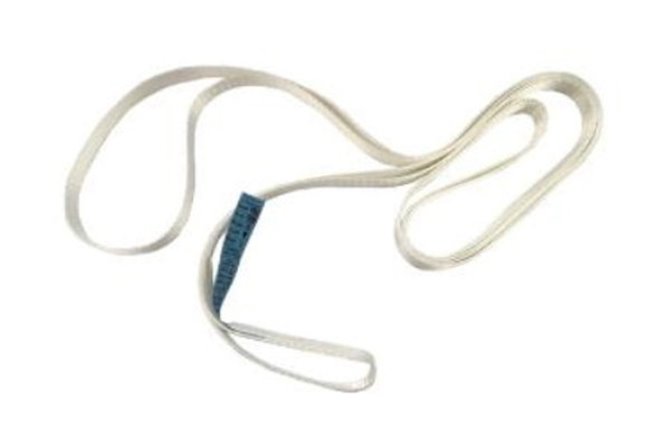
2. Handling - Lifting Equipment
The sling should be pre-installed in all lifting holes when the panel arrives at the worksite. The sling is secured with cable ties so that they never come out of their lifting holes. All lifting slings should be connected to the lifting device according to the label markings, see also pictures.
There should be no visible damage or defects on the sling during lifting. If such damage or defects are present, the sling should not be used. The sling should not be exposed to chemicals; if this occurs, the sling should be discarded. Furthermore, there should be no knots on the sling during lifting.
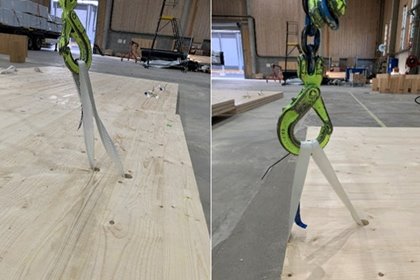
3. Lifting Capacity – Sling
The lifting capacity of the sling is indicated on the sling’s label, see below. Upon delivery to the worksite, the correct sling is pre-installed on each panel.
Note: All pre-installed slings must be used when lifting the panels.
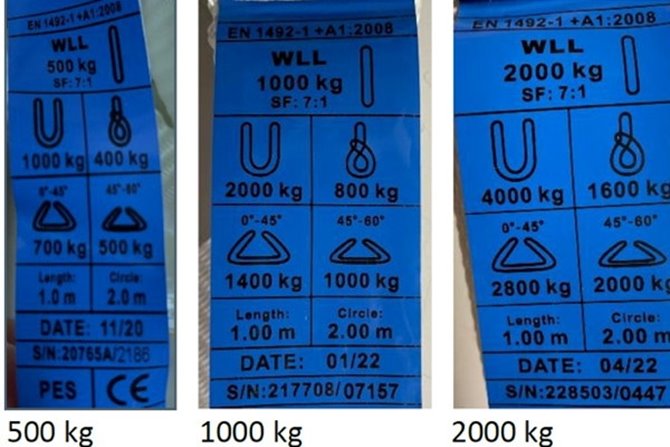
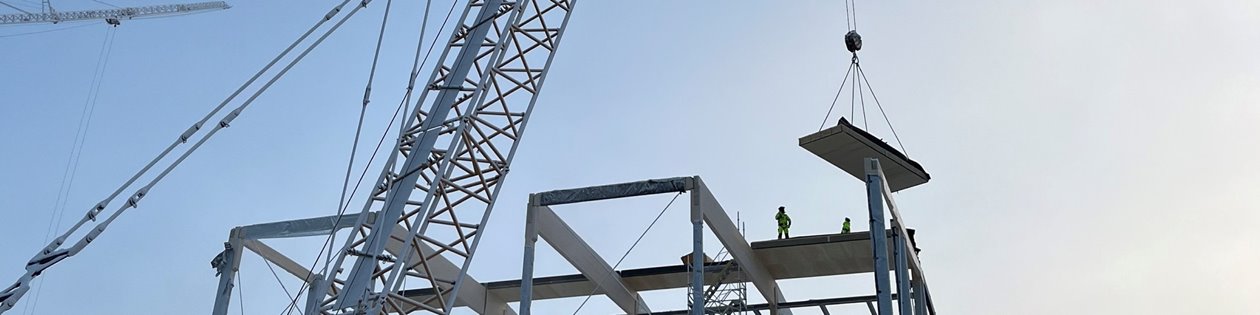
Würth transport anchor
Information and capacity values are taken from Würth’s user instructions and load tables. The instructions apply to lifting panels during assembly at the construction site, and the lifting capacity assumes that load distributors are used.
These instructions should be seen as a summary of Würth’s instructions. Södra is not responsible for incidents that occur due to the operator not following the manufacturer’s instructions.
- It's important that the operator is trained in the use of this lifting system and never performs lifting operations without ensuring work safety.
- The dimensioning and placement of screws are based on the vibration coefficient (φ = 1.1), which depends on the lifting conditions (type of crane and lifting speed). Under other lifting conditions, the capacity per lifting screw may be lower. The construction site is responsible for ensuring that lifting is performed safely concerning the conditions at the construction site.
- All lifts are dimensioned on the condition that load distributors are used during lifting so that all lifting points can be accounted for.
1. Intended Products
Lifting equipment: Würth transport anchor – For lifting and transporting prefabricated elements up to 1.3 tons, article number 018400013.
Screw: Würth ASSY® 4 Kombi T T6S – Lifting/transport screw for wooden elements, article numbers 015871091, 0158712121, and 0158712161.
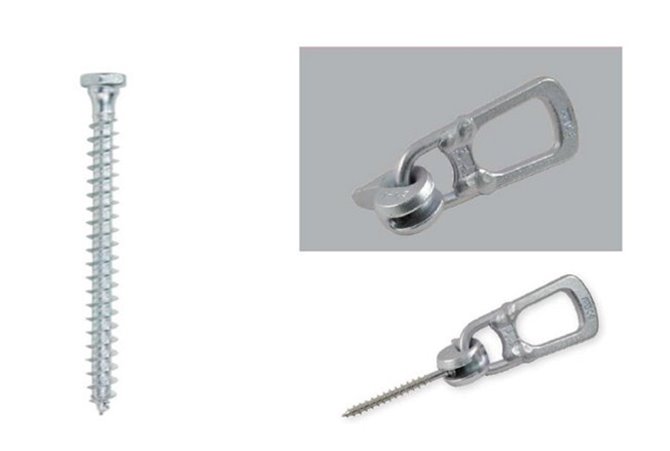
2. Maintenance – Lifting Equipment
The condition of the lifting yoke must be inspected by the operator before each use. Suspected damage to the lifting equipment, such as cracks, wear, deformations, etc., must be reported to the production management immediately, and the affected lifting equipment must be taken out of service.
The safety officer is responsible for ensuring that the lifting equipment, including the associated chain link, is continuously inspected and that the instructions are followed.
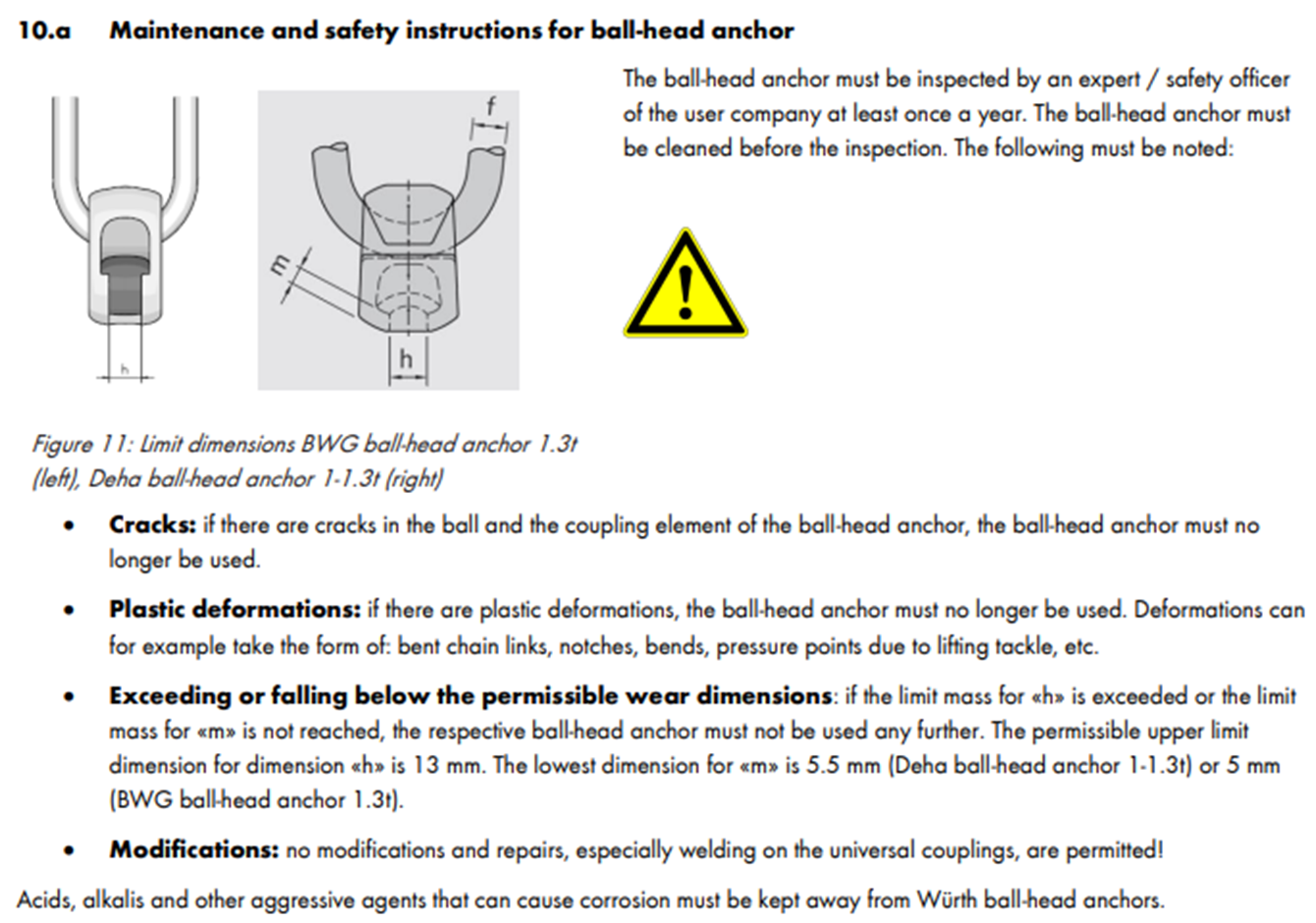
3. Handling – Lifting Equipment
The head/ball anchor of the lifting equipment is fixed to the screw by rotating it all the way until the stop of the equipment is parallel to the panel surface, see illustration 1. Disconnection is done in reverse order.
If the handled panel tilts during lifting, the stop of the head/ball anchor must be in the upward tilt, according to illustration 2. Otherwise, the lifting equipment risks rotating and then detaching from the screw.
The lifting capacity of the lifting equipment at 1.3 tons is much higher than that of the screw, see point 5 “Lifting Capacity – Screw”, which means that the screw is the part that sets the limitations for how large a CLT panel can be lifted.
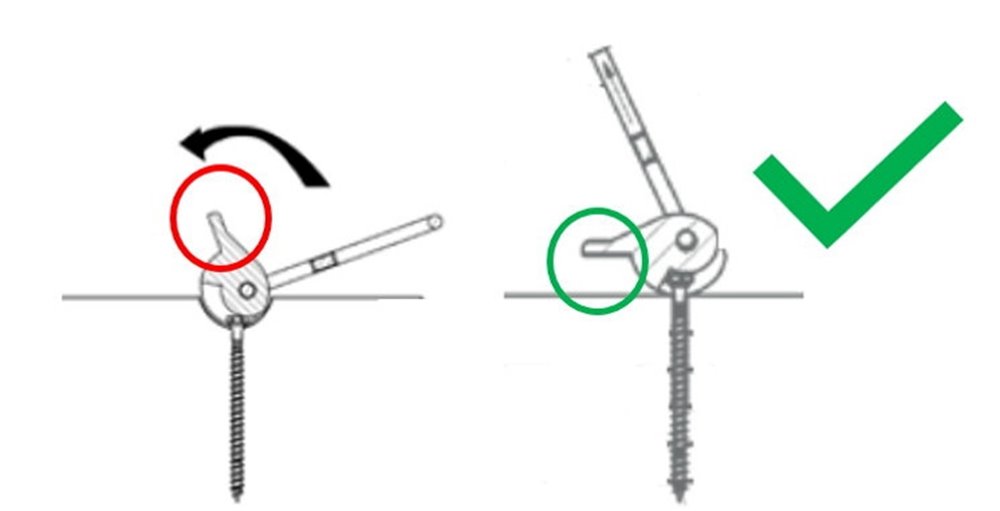
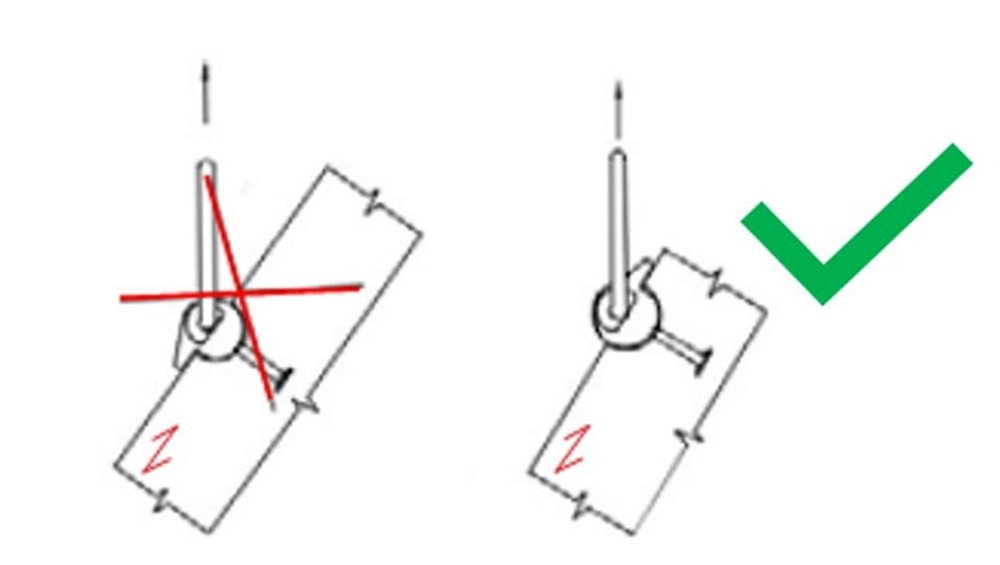
4. Maintenance – Screw
The screws are intended for single use, i.e., the manufacturer takes no responsibility for the screw’s capacity if reused. The operator is responsible for ensuring that the screws used during lifting are in satisfactory condition concerning, e.g., cracks, wear, deformations, etc. The screw can be used for multiple lifts if it remains in the CLT panel between lifts and the lift meets the applicable requirements, e.g., type of crane.
5. Handling – Screw
The screws are pre-installed upon delivery to the worksite; all screws must be used during lifting. When installing your own screws, the screws may only be attached perpendicular to the wood grain direction, i.e., screws must not be used in the end grain of the panel. When installing screws yourself, the construction site is responsible for following Würth’s instructions.
6. Lifting Capacity – Screw
The dimensioning and placement of screws in the panels are carried out in the factory before delivery to the construction site. All screws must be used during lifting. The screws must not be moved or partially unscrewed without the operator considering any changed conditions for lifting. The operator at the construction site is then responsible for following Würth’s instructions.
The lifting angle β must be in the range of 0° ≤ β ≤ 45°, see illustration 3. The highest capacity of the lifting equipment is when the lifting angle β = 0°, then the capacity decreases as the angle increases. With countersunk holes (diameter 70 mm, depth 30 mm), the screw’s capacity is the same as at β = 0° regardless of the angle β, but the maximum angle β = 45° applies.
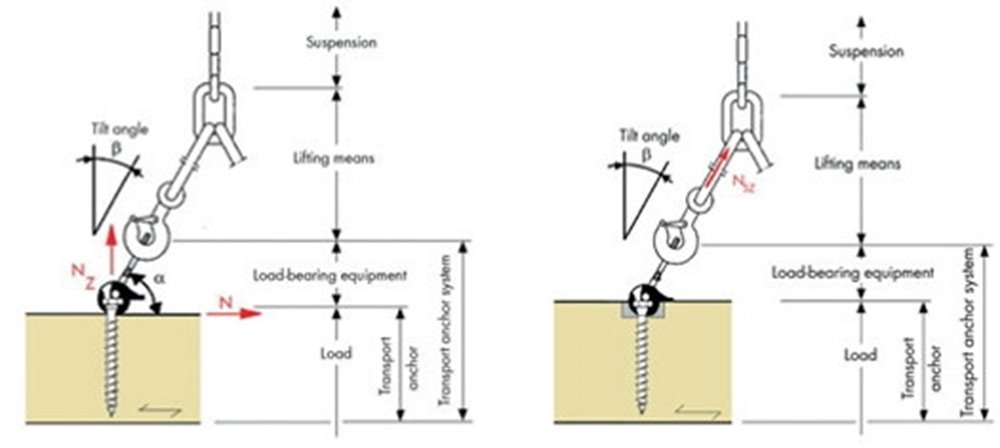