Innovation in paper pulp and dissolving pulp
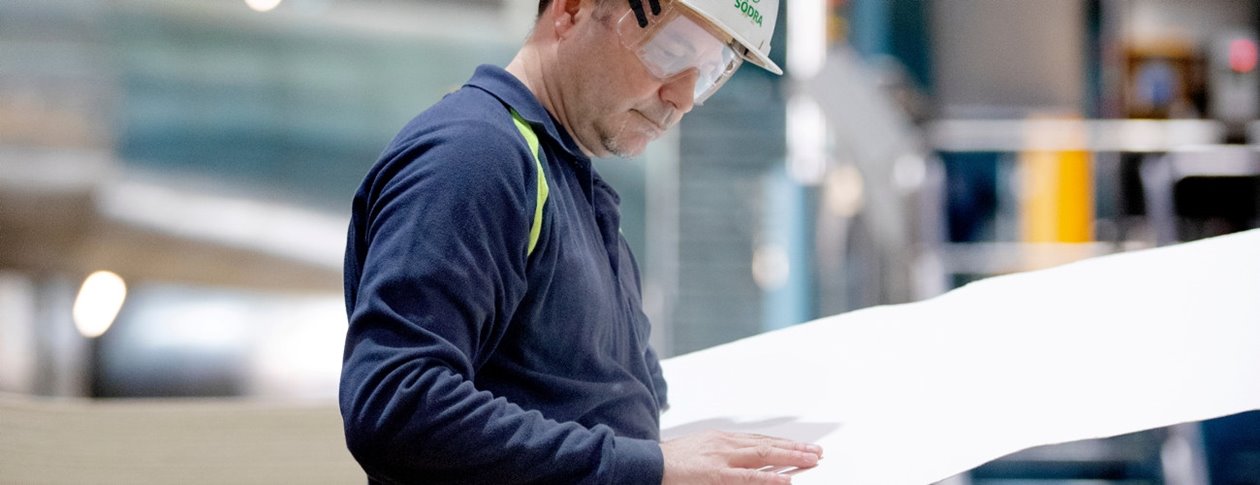
Product development for paper pulp
In the paper pulp area, development is taking place to optimise and further develop products and processes in order to improve quality and the resource-efficiency of mills. A key component of this product development is partnerships with customers. Customer needs are driving the development and placing demands on Södra’s product portfolio.
Partnerships with customers take place in various technical collaborations where the focus lies on implementing new or improved products, or optimising the customer’s processes. Replacing baling wire with paper tape is one example of a solution that improves both the safety and the viability of the customer’s process. Another example is Södra’s proprietary system for quality control and quality data for customers, where online data is combined with models for predicting paper properties to provide a frequent and robust system for direct feedback to Södra’s own production processes and to customers.
These continuous efforts with process development are focused on increasing the number of resource-efficient processes that can boost capacity and improve energy and chemical efficiency. Södra also contributes to industry-wide development in these areas, in addition to internal work.
Product development is also taking place within packaging, with the aim of replacing plastic with fibre. By using conversion technologies in both wet and dry-moulding, fibre-based alternatives can be manufactured with low CO₂ emissions and low energy consumption and used to replace plastic packaging in a range of segments, including food, electronics and beauty products.
Textiles from forest fibres
Södra has been producing dissolving pulp since 2012. The pulp is used to make cellulose-based textile fibres, such as viscose and lyocell. There is a great deal of interest in using forest-based fabrics to replace synthetic fibres and cotton. In addition, textile companies and consumers are increasingly requesting traceability across the entire value chain, from pulp production via all producer stages to the finished textile product. This is driving development and demand, and imposing new requirements on our dissolving pulp.
To further develop Södra’s dissolving pulp, close collaboration with customers is taking place in product and process development.
Textile recycling contributing to climate transition
Södra has also developed the OnceMore® technique for recycling textiles. Only a negligible proportion of the global production of clothing and textiles is recycled, the vast majority is either incinerated or sent to landfill. Södra was first in the world to introduce large-scale recycling of textile fibres from blended fabrics (polycottons).
The recycled textiles are used to make new dissolving pulp, which can then become new viscose and lyocell. The technique is a unique solution that enables circular flows in the fashion and textile industry. Swedish innovation and a willingness to contribute to the necessary climate transition can now be a game changer at global level.
The Södra Research Foundation is funding a project with RISE and Chalmers to further develop textile recycling.